Reduce downtime and fuel consumption.
Enhance engine performance and reduce emissions, all while maintaining a safer, healthier workplace.
The Epura system is the award-winning air purification technology by Propulsa Innovations that outperforms traditional systems even in the dustiest environments. Expect constant, high-quality air supply in your cabins and engines without the need for regular filter changes.
Applications

Trucks

Loaders

Excavators

Dozers
For engines and cabins.
Key Benefits & Features
Fuel efficiency and performance
Maintains air volume for optimal power, fuel economy (up to 10% improvement), and emissions.
Self-cleaning system using low-frequency sound waves
Eliminate the hassle of frequent filter changes, preventing work interruptions, and reducing maintenance costs.
Comprehensive protection
Installed upstream from the OEM filter, it adds protection for your engine without affecting the warranty.

Additional Benefits
-
Measures pressure differential across the filter and initiates cleaning at a set restriction limit
-
Activated charcoal filtration option available
-
Replaces and eliminates the need for existing pre-cleaners
-
Can be installed directly on the filter box housing
-
Offers fast ROI and simple installation
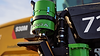
Annual Savings
Equipment: Komatsu WA 900
Epura: EPU-G5-D15 (Dual 10”) PM
Cost: $550 @ 250 HRS
Fuel Efficiency: 5%
Emissions Reductions: 2%

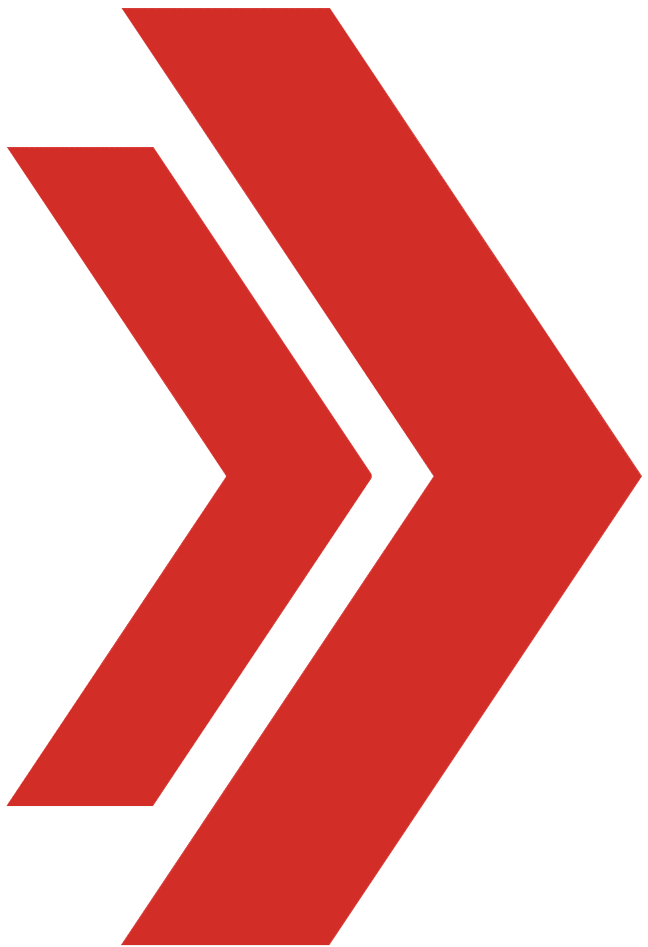


1. Self-Cleaning Head
Epura uses low-frequency sound waves to eject dust particles without damaging the filter.
2. High Quality Filter
Unique cartridge and moisture resistant media tailored for the Epura system, ensuring mining-worthy filtration.
3. Air Intake
The point of entry for dirty air and ejection of accumulated dust.
4. Operator Interface
Allows monitoring of the system pressure status, measuring pressure differential across the filter and initiating cleaning at a set restriction limit.
How it Works

1
Install upstream of the original air filter. Dirty air enters filter, 97% cleaner air to OEM filter.

2
Pressure differential is monitored. When set limit is reached operator is warned. When engine is off or at idle, operator sends signal to clean.
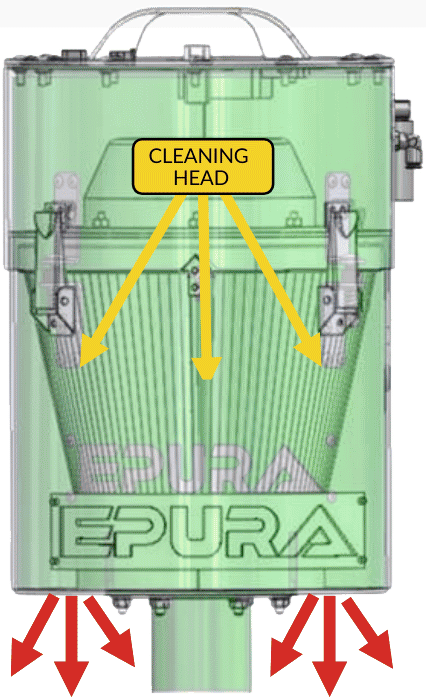
3
Patented infrasound cleaning cycle is initiated. Dust is ejected at the base of the unit.
Filter Restriction vs Fuel Consumption
-
As dust restricts air flow the pressure differential increases
-
Reduced air for combustion multiplies inefficiencies
-
Condition persists until filter is replaced or cleaned
For full details - see brochure

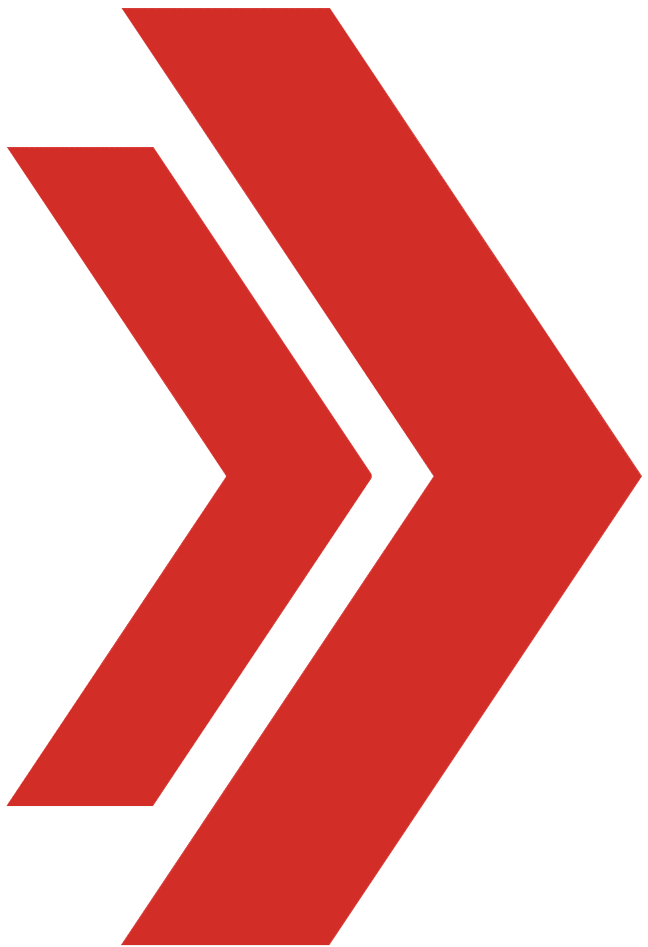


Case Study
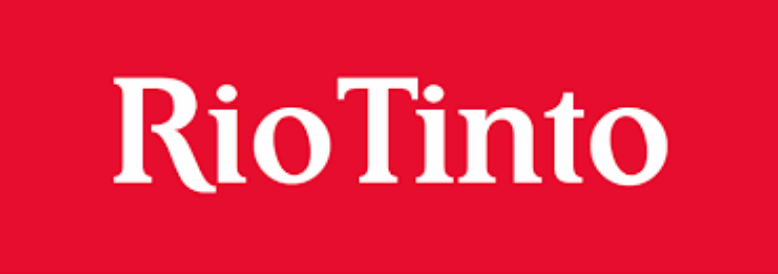
Results
Rio Tinto Saguenay–Lac-Saint-Jean has seen impressive benefits from Epura systems, including significant reduction in maintenance expenses for its vehicles and a return on investment in just 10 weeks.


-
More than $21,000/year/vehicle in savings related to engine filter changes (filters and labour)
-
More than $38,000/year/vehicle in savings related to cabin filter changes
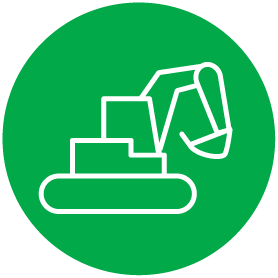
-
More than $60,000 in savings on expenses related to time lost to maintenance
-
Vehicles require no filter maintenance

-
Lower fuel use and fewer pollutant emissions for each vehicle
-
Complies with existing health and safety standards
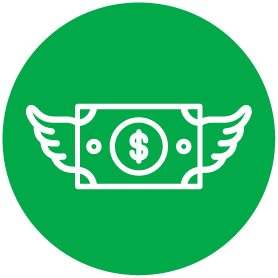
-
More than $2,500 in savings on assorted expenses related to premature wear
-
More than $3,600/year/vehicle in savings on engine oil
How it Saves
Filter Savings

All associated costs with the air filter portion of the PM are eliminated by eliminating the need to replace the filters.

Filter cost and inventory, labour time and production availability may all be factored.
Fuel Savings

Controlling pressure differential reduces the amount of time the equipment operates in high fuel consumption and low power band.
-
Up to 10% fuel efficiency
-
Maintains optimal power from the engine 80-90% of the time vs 20-50% with regular filters
Air Filter Restriction vs Fuel Consumption
PM @500 HRS

Air Filter Restriction vs Fuel Consumption
PM @250 HRS

System Sizes
Model | A mm (in) | B mm (in) | C mm (in) | D mm (in) | E mm (in) | F mm (in) | G mm (in) |
---|---|---|---|---|---|---|---|
EPU-G5-M15 | 650 (25-1/2) | 527 (20-3/4) | 546 (21-1/2) | 254 (10) | 149 (5-7/8) | 203 (8) | 203 (8) |
EPU-G5-M12 | 572 (22-1/2) | 443 (17-7/16) | 464 (18-1/4) | 203 (8) | 111 (4-3/8) | 152 (6) | 203 (8) |
EPU-G5-M10 | 523 (20-5/8) | 391 (15-3/8) | 410 (16-1/8) 152 (6) | 152 (6) | 105 (4-1/8) | 108 (4-1/4) | 152 (6) |
EPU-G5-M08 | 422 (16-5/8) | 302 (11-7/8) | 324 (12-3/4) | 102 (4) | 64 (2-1/2) | 95 (3-3/4) | 127 (5) |
Technical Data Chart
Model | Motor power in kW (hp) | Displacement in litres (cu in) | Flow in m³/h (CFM) | Tension (Volt) | Intensity (Ampere) |
---|---|---|---|---|---|
EPU-G5-M15 | 360 (500) | < 18 (1100) | < 1550 (1160) | 12 Vcc / 24 Vcc | 10 A (During cleaning) |
EPU-G5-M12 | <270 (375) | <12 (732) | <1360 (800) | 12 Vcc / 24 Vcc | 10 A (During cleaning) |
EPU-G5-M10 | < 180 (249) | < 8 (488) | < 700 (523) | 12 Vcc / 24 Vcc | 10 A (During cleaning) |
EPU-G5-M08 | < 98 (131) | < 4 (245) | < 375 (220) | 12 Vcc / 24 Vcc | 10 A (During cleaning) |
*For larger engines, systems can be installed in parallel.
**For informational purposes only. Data may vary depending on the application and dust load.
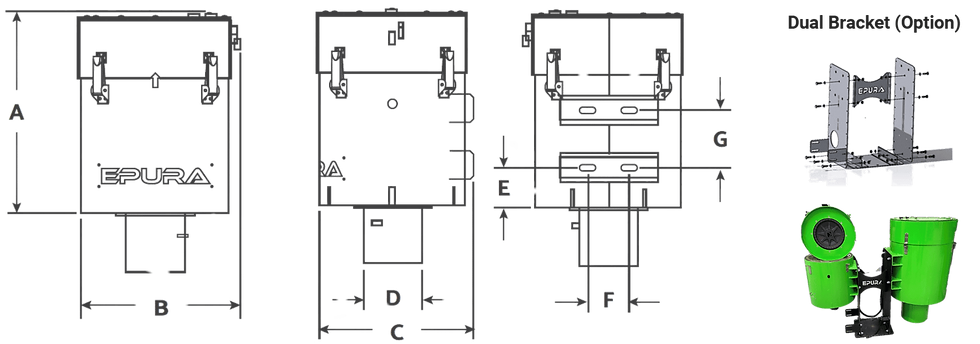